The journey from farm to fork involves an intricate web of processes that most consumers never see. Food supply chain logistics orchestrates the complex movement of agricultural products through multiple stages – from harvesting and processing to packaging and distribution – ensuring fresh ingredients reach millions of tables worldwide. This sophisticated system requires precise coordination between farmers, manufacturers, distributors, and retailers to maintain product quality while meeting consumer demand.
The article delves into the complexities of the food supply chain logistics, emphasizing the critical link between farmers, manufacturers, distributors, and retailers. It highlights modern challenges such as managing perishability, transportation hurdles, and inventory complexities amid rising global demand. Advanced technologies, including IoT and blockchain, are transforming operations by improving traceability and compliance. Emphasis is placed on sustainability initiatives aimed at reducing waste and enhancing environmental responsibility, ultimately reshaping food distribution systems to meet contemporary consumer needs.
Modern food logistics faces unprecedented challenges as global populations grow and consumer expectations evolve. Supply chain disruptions can ripple through entire networks, affecting everything from grocery store shelves to restaurant menus. Companies must navigate perishable inventory management, temperature-controlled transportation, and stringent food safety regulations while optimizing costs and delivery times.
Understanding the mechanics behind food supply chain logistics reveals why certain products cost more, how seasonal availability affects pricing, and what happens when disruptions occur. These systems directly impact food security, waste reduction, and the overall efficiency of feeding communities across the globe.
Table of Contents
Understanding Food Supply Chain Logistics
Food supply chain logistics encompasses the intricate network of processes, systems, and stakeholders responsible for moving food products from production facilities to consumers’ tables while maintaining quality, safety, and efficiency throughout the journey. This complex orchestration involves coordinating multiple touchpoints across vast geographical distances, with 72% of global food transportation occurring through integrated supply networks according to recent industry analysis.
Key Components and Stakeholders
The food supply chain ecosystem operates through interconnected components that each play distinct roles in ensuring product quality and accessibility. Primary producers, including farmers and agricultural cooperatives, serve as the foundation of food distribution networks. These stakeholders manage initial harvesting, basic processing, and preparation of raw materials for transportation to processing facilities.
Food manufacturers and processors transform raw agricultural products into consumer-ready goods through various production methods. Companies like Tyson Foods, Nestlé, and Unilever operate extensive processing facilities that handle billions of pounds of food products annually. These facilities must maintain strict food safety standards and HACCP compliance protocols to ensure product integrity throughout manufacturing processes.
Distribution centers and warehouses form the backbone of food storage solutions across the supply chain. These facilities utilize sophisticated warehouse management systems to track inventory levels, monitor product freshness, and coordinate outbound shipments. Modern distribution centers employ automated storage and retrieval systems that can process up to 50,000 cases per hour while maintaining temperature-controlled environments for perishable goods.
Transportation providers specialize in moving food products through various modes including refrigerated trucks, rail cars, and shipping containers. The cold chain infrastructure represents a critical component, with temperature-controlled transportation accounting for approximately 15% of total logistics costs in the food industry. Companies must maintain precise temperature ranges during transit to preserve product quality and extend shelf life.
Retailers and foodservice operators serve as the final link before products reach consumers. Major grocery chains like Walmart, Kroger, and Amazon Fresh operate their own distribution networks, while smaller retailers rely on third-party logistics providers for supply chain management. These operations require sophisticated inventory management systems to balance product availability with minimizing waste from expired goods.
Technology providers supply essential systems for traceability in food logistics, enabling real-time monitoring of product movement and quality parameters. Advanced tracking systems utilize RFID tags, IoT sensors, and blockchain technology to create comprehensive audit trails from farm to fork. These systems help companies respond quickly to food safety incidents and maintain regulatory compliance in food supply operations.
Regulatory bodies and certification organizations oversee food safety standards and ensure compliance with health regulations. The FDA, USDA, and various international food safety authorities establish guidelines that all stakeholders must follow. Third-party auditing companies verify compliance with these standards through regular inspections and certifications.
From Farm to Fork: The Complete Journey
The food supply chain journey begins at agricultural production sites where farmers cultivate crops and raise livestock according to specific quality standards. Initial harvesting and collection processes must maintain product integrity while preparing goods for transportation to processing facilities. Fresh produce requires immediate cooling and proper handling to preserve nutritional value and extend shelf life.
Processing facilities receive raw agricultural products and transform them into consumer-ready formats through various manufacturing techniques. These operations include cleaning, sorting, packaging, and labeling products according to regulatory requirements. Processing plants must maintain strict temperature controls and sanitation protocols to prevent contamination and ensure food safety throughout production cycles.
Quality control measures at processing facilities involve multiple inspection points where products undergo testing for contaminants, nutritional content, and compliance with established standards. Automated inspection systems can identify defects and foreign objects at rates exceeding 99.5% accuracy, significantly reducing the risk of compromised products entering the supply chain.
Packaging operations prepare products for distribution by applying protective materials and labeling that includes nutritional information, expiration dates, and traceability codes. Modern packaging incorporates smart technology such as time-temperature indicators and freshness sensors that provide real-time quality information throughout the supply chain. Sustainable packaging solutions have become increasingly important, with 68% of food manufacturers implementing eco-friendly packaging materials by 2024.
Distribution networks coordinate the movement of packaged products from processing facilities to regional distribution centers. These operations require precise scheduling and route optimization to minimize transportation costs while ensuring product freshness. Advanced logistics software analyzes multiple variables including traffic patterns, weather conditions, and delivery schedules to optimize distribution efficiency.
Cold chain management maintains proper temperature conditions for perishable products throughout transportation and storage. Refrigerated vehicles and temperature-controlled warehouses use sophisticated monitoring systems to track environmental conditions continuously. Disruptions in cold chain integrity can result in significant product losses, with temperature excursions accounting for approximately 30% of food waste in developed countries.
Warehouse operations at distribution centers involve receiving, storing, and preparing products for final delivery to retail locations. These facilities use automated systems for inventory management, order picking, and loading operations. Modern warehouses can process thousands of product lines simultaneously while maintaining accurate inventory records and ensuring proper stock rotation.
Last-mile delivery in food industry represents the final transportation stage from distribution centers to retail locations or directly to consumers. This phase requires careful coordination to ensure products arrive fresh and undamaged. E-commerce growth has created new demands for direct-to-consumer delivery services, with online grocery sales increasing by 45% in 2024.
Retail operations receive products from distribution centers and prepare them for consumer purchase through various merchandising and display techniques. Grocery stores use sophisticated inventory management systems to track product movement and optimize stock levels. Point-of-sale systems provide real-time data on consumer purchasing patterns, enabling retailers to adjust inventory and pricing strategies accordingly.
Value-added logistics services enhance the basic transportation and storage functions by providing additional benefits such as custom packaging, product assembly, and promotional support. These services help manufacturers differentiate their products and respond to specific customer requirements. Companies offering value-added services typically achieve 15-20% higher profit margins compared to basic logistics providers.
Risk management in food distribution involves identifying potential disruptions and implementing contingency plans to maintain supply chain continuity. Common risks include weather events, equipment failures, labor shortages, and regulatory changes. Effective risk management strategies include diversifying supplier networks, maintaining safety stock levels, and developing alternative transportation routes.
Traceability systems track products throughout the entire supply chain journey, creating detailed records of origin, processing, and distribution activities. These systems enable rapid identification and isolation of contaminated products during food safety incidents. Blockchain technology has emerged as a leading solution for creating immutable traceability records, with major food companies implementing blockchain-based tracking systems to enhance transparency and accountability.
Food logistics innovation continues to drive improvements in efficiency, sustainability, and product quality throughout the supply chain. Emerging technologies include autonomous vehicles for transportation, artificial intelligence for demand forecasting, and advanced sensors for real-time quality monitoring. These innovations help companies reduce costs, minimize waste, and improve customer satisfaction.
Data analytics platforms process vast amounts of information from supply chain operations to identify trends, optimize processes, and predict potential issues. Machine learning algorithms analyze historical data to improve demand forecasting accuracy and reduce inventory holding costs. Companies using advanced analytics typically achieve 10-15% improvements in operational efficiency compared to traditional methods.
Sustainability initiatives focus on reducing environmental impact throughout the food supply chain journey. These efforts include optimizing transportation routes to reduce fuel consumption, implementing energy-efficient warehouse operations, and reducing packaging waste. Many companies have established specific sustainability targets, with 82% of major food manufacturers committing to carbon-neutral operations by 2030.
Regulatory compliance in food supply requires adherence to multiple standards and regulations throughout the entire journey from farm to fork. Companies must maintain detailed documentation of all processes and implement corrective actions when deviations occur. Regular audits and inspections ensure ongoing compliance with food safety standards and help identify areas for improvement.
Consumer demand for transparency and product information has driven the development of enhanced labeling and communication systems. QR codes and mobile applications provide consumers with access to detailed product information including origin, processing methods, and nutritional content. This transparency helps build trust and allows consumers to make informed purchasing decisions.
The integration of multiple stakeholders and systems throughout the farm-to-fork journey requires sophisticated coordination and communication mechanisms. Supply chain management platforms enable real-time information sharing between partners, improving visibility and enabling rapid response to disruptions. These systems help reduce lead times, minimize inventory costs, and improve overall supply chain performance.
Quality assurance programs span the entire supply chain journey, with checkpoints at each stage to verify product integrity and compliance with standards. These programs include incoming material inspections, in-process monitoring, and finished product testing. Comprehensive quality assurance helps prevent defective products from reaching consumers and maintains brand reputation.
Temperature monitoring systems track environmental conditions throughout the cold chain to ensure product quality and safety. Advanced sensors provide continuous monitoring with automatic alerts when conditions deviate from specified ranges. This technology helps prevent spoilage and extends product shelf life, reducing waste and improving profitability.
Inventory optimization balances product availability with storage costs throughout the supply chain. Advanced forecasting systems analyze demand patterns, seasonal variations, and promotional activities to determine optimal inventory levels. Companies using sophisticated inventory management typically achieve 20-25% reductions in carrying costs while maintaining service levels.
Cross-docking operations at distribution centers enable direct transfer of products from inbound to outbound transportation without intermediate storage. This approach reduces handling costs and shortens delivery times for products with predictable demand patterns. Cross-docking facilities can process up to 80% of products without storage, significantly improving efficiency.
Performance metrics throughout the supply chain journey include delivery accuracy, product quality, cost efficiency, and customer satisfaction. Companies track these metrics continuously to identify improvement opportunities and benchmark performance against industry standards. Leading performers typically achieve 99.5% order accuracy and 95% on-time delivery rates.
Collaboration between supply chain partners enhances overall system performance through shared information, coordinated planning, and joint problem-solving. Strategic partnerships enable companies to leverage complementary capabilities and achieve economies of scale. Collaborative relationships typically result in 10-15% cost reductions and improved service levels.
The food supply chain journey requires continuous adaptation to changing market conditions, consumer preferences, and regulatory requirements. Companies must maintain flexibility to adjust operations while preserving product quality and safety standards. This adaptability ensures long-term viability and competitiveness in the dynamic food industry environment.
Current Challenges in Food Supply Chain Logistics
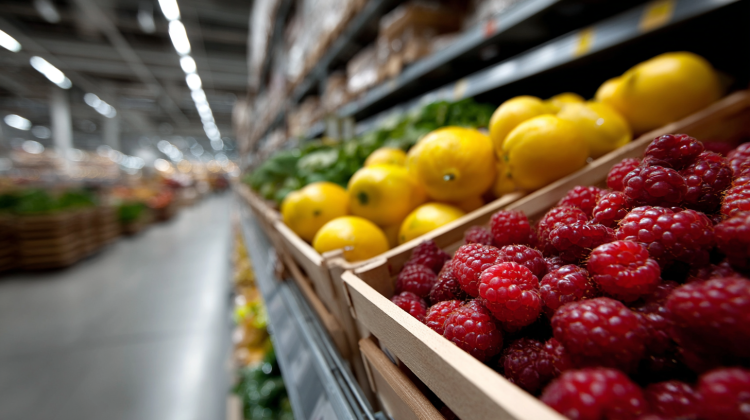
Food supply chain logistics encounters three primary disruptions that impact global food distribution networks. These challenges create cascading effects throughout the entire system, from agricultural production to consumer delivery.
Perishability and Temperature Control
Temperature-sensitive products require continuous monitoring and specialized handling throughout their journey from farm to consumer. Dairy products, fresh meat, and produce demand strict temperature ranges to maintain safety standards and prevent spoilage. Cold chain management represents one of the most critical aspects of food distribution, yet equipment failures and temperature fluctuations occur frequently during transport.
Refrigerated carriers face significant technical challenges maintaining consistent temperatures across long-distance routes. Temperature deviations of just 2-3 degrees Celsius can compromise product integrity and create food safety risks. Equipment malfunctions during transport result in entire shipments becoming unsalable, leading to substantial financial losses for suppliers and distributors.
Real-time monitoring systems now track temperature conditions throughout the supply chain journey. IoT sensors provide continuous data streams that alert logistics managers to potential temperature breaches before products become compromised. These monitoring systems integrate with warehouse management systems to provide comprehensive visibility across the entire cold chain network.
Specialized refrigerated carriers have developed advanced cooling technologies to address temperature control challenges. Multi-zone refrigeration systems allow different product categories to maintain their optimal temperature ranges within the same transport vehicle. These innovations reduce transportation costs while maintaining strict temperature requirements for diverse product portfolios.
Food safety standards require detailed documentation of temperature conditions throughout the supply chain. HACCP compliance mandates continuous monitoring and record-keeping for all temperature-sensitive products. Regulatory inspections focus heavily on cold chain documentation, making temperature tracking systems essential for maintaining compliance.
Storage solutions at distribution centers incorporate advanced cooling technologies to extend product shelf life. Automated temperature monitoring systems trigger alerts when storage conditions deviate from acceptable ranges. These systems integrate with inventory management platforms to prioritize products approaching their expiration dates.
Traceability in food logistics becomes particularly important for temperature-sensitive products. Digital tracking systems record temperature data at every stage of the supply chain, creating comprehensive audit trails. This traceability enables rapid response to food safety incidents and helps identify the source of temperature-related quality issues.
Transportation and Distribution Hurdles
Geopolitical tensions disrupt established shipping routes and create uncertainty in international food trade. Trade restrictions and tariffs add complexity to sourcing strategies, forcing companies to develop alternative supplier networks. These disruptions particularly impact global food distribution networks that rely on specific geographic regions for key ingredients.
Climate-related disruptions have increased dramatically, with extreme weather events affecting transportation infrastructure. Flooding, hurricanes, and severe storms damage roads, ports, and rail systems used for food distribution. These weather-related disruptions create bottlenecks that can last weeks or months, forcing logistics managers to develop contingency plans.
Labor shortages across the transportation sector impact delivery schedules and increase operational costs. Truck driver shortages have reached critical levels, with the American Trucking Association reporting a shortage of over 80,000 drivers. These shortages create delays in food distribution and increase transportation costs throughout the supply chain.
Route disruptions require logistics managers to develop flexible transportation strategies. Alternative routing systems use predictive analytics to identify potential disruptions before they impact delivery schedules. These systems analyze weather patterns, traffic conditions, and infrastructure maintenance schedules to recommend optimal routes.
Digital transformation initiatives help transportation providers improve efficiency and reduce costs. Transportation Management Systems (TMS) integrate with GPS tracking and route optimization software to maximize vehicle utilization. These platforms provide real-time visibility into shipment status and enable proactive management of potential delays.
Supplier diversification strategies reduce dependency on single transportation routes or carriers. Companies develop relationships with multiple transportation providers across different geographic regions. This diversification creates redundancy that helps maintain delivery schedules when primary transportation options become unavailable.
Infrastructure limitations in rural areas create challenges for food distribution networks. Poor road conditions and limited access to major highways increase transportation costs and delivery times. These limitations particularly impact small-scale producers who lack access to efficient transportation networks.
Fuel price volatility affects transportation costs and creates uncertainty in logistics planning. Fluctuating fuel prices impact route selection and carrier selection decisions. Transportation providers develop fuel surcharge programs to manage these cost variations, but these surcharges ultimately increase food distribution costs.
Inventory Management Complexities
Balancing inventory levels against product perishability creates ongoing challenges for food distribution networks. Holding excessive inventory increases storage costs and waste, while insufficient inventory levels result in stockouts and lost sales. This balance becomes particularly difficult with seasonal products that have limited harvest windows.
Demand forecasting for perishable products requires sophisticated analytics that consider multiple variables. Weather patterns, seasonal trends, and consumer preferences all impact demand patterns. Traditional forecasting methods often fail to account for the complex interactions between these variables, leading to inventory imbalances.
Approximately 30% of food produced globally is lost or wasted annually, with significant portions occurring during storage and distribution. Inefficient inventory practices contribute substantially to this waste, particularly for products with short shelf lives. Inventory management systems must account for product deterioration rates and optimize turnover to minimize waste.
Advanced ERP systems integrate inventory management with demand forecasting and transportation planning. These integrated platforms provide real-time visibility into inventory levels across multiple locations. Automated reorder systems trigger replenishment orders based on predefined parameters that account for product shelf life and demand patterns.
Transportation Management Systems (TMS) connect inventory management with delivery scheduling to optimize product flow. These systems prioritize shipments based on product expiration dates and customer requirements. Integration between inventory and transportation systems reduces handling time and improves product freshness.
AI-driven demand forecasting analyzes historical sales data, weather patterns, and market trends to predict future demand. Machine learning algorithms identify patterns that traditional forecasting methods might miss. These predictive models help inventory managers make informed decisions about stock levels and product mix.
Automated warehouse management systems reduce manual handling and improve inventory accuracy. Robotic systems handle product movement and storage, reducing labor costs and improving efficiency. These automated systems integrate with inventory management platforms to provide real-time stock updates.
Risk management in food distribution requires contingency planning for supply disruptions. Inventory managers develop safety stock strategies that account for potential supplier delays and transportation disruptions. These strategies balance the cost of holding additional inventory against the risk of stockouts.
Value-added logistics services help companies optimize their inventory management strategies. Third-party logistics providers offer specialized inventory management services that include demand forecasting, stock optimization, and waste reduction programs. These services enable companies to focus on their core business activities while improving inventory efficiency.
Food storage solutions continue evolving to extend product shelf life and reduce waste. Modified atmosphere packaging and controlled atmosphere storage help preserve product quality. These technologies enable longer storage periods and provide more flexibility in inventory management.
Regulatory compliance in food supply chains requires detailed inventory tracking and documentation. Traceability systems must track product movement from supplier to consumer, including storage conditions and handling procedures. These compliance requirements add complexity to inventory management systems but provide essential food safety protections.
Last-mile delivery in food industry creates unique inventory management challenges. Direct-to-consumer delivery requires inventory positioning closer to end customers. This distribution model requires different inventory strategies compared to traditional retail distribution channels.
Business growth strategies for food logistics companies increasingly focus on inventory optimization technologies. Companies invest in advanced analytics and automation to improve inventory turnover and reduce waste. These investments help companies maintain profitability while meeting growing consumer demand for fresh, high-quality products.
Technology Solutions Transforming Food Logistics
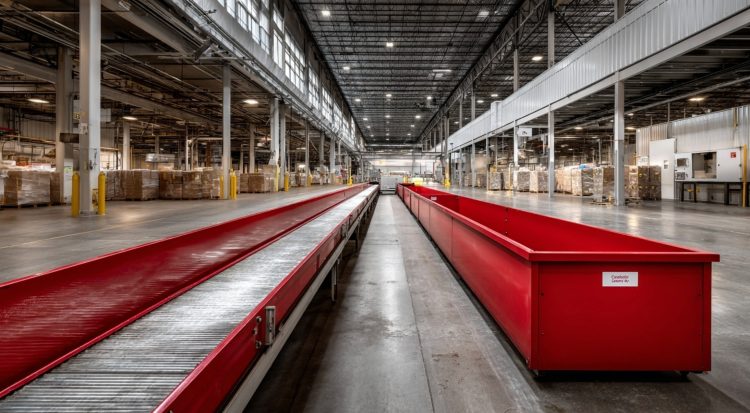
Advanced technology solutions are revolutionizing food distribution networks by addressing critical challenges in efficiency, traceability, and safety. These innovations create seamless connections between producers, processors, distributors, and retailers while ensuring regulatory compliance and consumer trust.
Cold Chain Management Systems
Cold chain management systems represent the backbone of modern food storage solutions, maintaining precise environmental conditions throughout the entire distribution process. These sophisticated systems utilize automated sensors and control mechanisms to preserve temperature-sensitive products from initial processing through final delivery.
Temperature monitoring equipment now incorporates advanced algorithms that detect fluctuations within 0.1-degree increments, preventing spoilage before it occurs. Modern cold storage facilities employ multi-zone temperature controls that accommodate different product requirements simultaneously. Fresh produce requires temperatures between 32-40°F, while frozen goods maintain optimal quality at -10°F to 0°F.
Humidity control systems work alongside temperature management to create optimal storage environments. These systems maintain relative humidity levels between 85-95% for fresh vegetables and 80-85% for dairy products. Automated ventilation systems circulate air at controlled rates, preventing moisture buildup that leads to bacterial growth and product deterioration.
Energy-efficient refrigeration technology has reduced operational costs by 30% while improving temperature consistency. Variable-speed compressors adjust cooling capacity based on actual demand, minimizing energy waste during low-activity periods. Smart defrost systems activate only when necessary, maintaining consistent temperatures while reducing energy consumption.
Real-time monitoring dashboards provide warehouse managers with immediate visibility into environmental conditions across multiple storage zones. These systems generate automated alerts when parameters exceed predetermined thresholds, enabling rapid intervention before product quality suffers. Historical data analysis helps identify patterns that predict equipment maintenance needs, reducing unexpected failures.
Temperature mapping studies conducted in modern facilities reveal that strategic sensor placement ensures comprehensive coverage of critical storage areas. These studies identify potential hot spots or cold zones that could compromise product integrity, allowing for corrective adjustments before inventory placement.
Specialized transportation vehicles now integrate seamlessly with facility management systems, maintaining cold chain integrity during transit. These vehicles feature independent temperature zones that accommodate mixed loads of products with varying temperature requirements. GPS tracking combined with temperature monitoring provides complete visibility throughout the distribution journey.
IoT and Real-Time Tracking
Internet of Things technology creates interconnected networks of sensors and devices that monitor food products throughout every stage of the supply chain. These systems provide continuous data streams that enable proactive decision-making and immediate response to potential issues.
RFID tags attached to individual products or shipping containers transmit location and condition data at regular intervals. These tags contain embedded sensors that monitor temperature, humidity, shock, and other environmental factors that affect product quality. Advanced RFID systems can store up to 8KB of data per tag, including product origin, processing dates, and quality certifications.
Wireless sensor networks deployed throughout warehouses and distribution centers create comprehensive monitoring coverage. These networks typically include 50-100 sensors per 10,000 square feet of storage space, ensuring no area remains unmonitored. Battery-powered sensors operate for 2-3 years without replacement, minimizing maintenance requirements.
Real-time data transmission enables immediate alerts when products experience adverse conditions. These systems can detect temperature deviations, excessive vibration during transport, or unauthorized access to secured storage areas. Automated notification systems send alerts to relevant personnel within 30 seconds of detecting anomalies.
Predictive analytics algorithms analyze historical data patterns to forecast potential disruptions before they occur. These systems identify trends in temperature fluctuations, equipment performance, and environmental conditions that typically precede quality issues. Machine learning models improve prediction accuracy over time, reducing false alarms by 40%.
Mobile applications provide field personnel with instant access to product information and condition data. Delivery drivers can verify product integrity before customer handoff, while warehouse workers receive real-time guidance on handling requirements. These applications support barcode scanning, photo documentation, and electronic signature capture.
Integration with existing warehouse management systems creates seamless data flow between tracking systems and inventory management. This integration eliminates manual data entry errors and provides complete visibility into product movement and condition throughout the facility.
Geofencing technology creates virtual boundaries around facilities and delivery zones, triggering automated actions when products enter or exit specific areas. These systems can automatically update inventory records, generate delivery confirmations, and initiate next-stage processing procedures.
Blockchain for Transparency
Blockchain technology establishes immutable records of food product journeys from farm to consumer, creating unprecedented transparency in food logistics operations. This distributed ledger system ensures that all stakeholders have access to verified information about product origin, processing, and distribution.
Each product entry in the blockchain contains detailed information including harvest dates, processing locations, quality test results, and handling procedures. This information cannot be altered or deleted once recorded, providing consumers and regulators with complete confidence in data integrity. Smart contracts automatically execute predetermined actions when specific conditions are met, reducing manual intervention and potential errors.
Supply chain participants contribute data at each stage of the process, creating a comprehensive record of product history. Farmers input harvest data, processors add production information, distributors record handling procedures, and retailers document final sale details. This collaborative approach ensures complete traceability while maintaining data security.
Rapid identification of contamination sources becomes possible through blockchain’s detailed tracking capabilities. When food safety issues arise, investigators can trace affected products back to their source within minutes rather than days or weeks. This capability significantly reduces the scope of product recalls and minimizes consumer exposure to contaminated products.
Authentication verification prevents counterfeit products from entering the supply chain by creating unique digital signatures for each legitimate item. These signatures cannot be replicated, ensuring that only authentic products reach consumers. This feature is particularly valuable for premium brands and organic products where authenticity commands higher prices.
Integration with IoT sensors creates a comprehensive record of environmental conditions throughout the supply chain. Temperature readings, humidity levels, and other sensor data are automatically recorded in the blockchain, providing irrefutable evidence of proper handling procedures. This integration supports HACCP compliance and regulatory audit requirements.
Consumer access to blockchain data through mobile applications enables informed purchasing decisions. Shoppers can scan product QR codes to view complete supply chain information, including origin farms, processing facilities, and transportation history. This transparency builds consumer trust and supports premium pricing for products with verifiable quality standards.
Regulatory compliance becomes more efficient through blockchain’s comprehensive documentation capabilities. Food safety inspectors can quickly verify compliance with regulatory requirements by reviewing blockchain records rather than manually auditing paper-based systems. This efficiency reduces inspection time and costs while improving accuracy.
Cross-border trade benefits from blockchain’s standardized documentation format, which facilitates customs clearance and regulatory approval processes. International shipments can be verified quickly without extensive paperwork, reducing delays and associated costs. This capability is particularly valuable for perishable products where time delays directly impact quality and profitability.
The integration of these technology solutions creates a synergistic effect that transforms food supply chain logistics beyond the capabilities of individual systems. Cold chain management systems provide the foundation for product preservation, while IoT networks monitor conditions continuously. Blockchain technology ensures that all data remains secure and verifiable, creating a transparent and trustworthy system for all stakeholders.
Warehouse management systems now incorporate these technologies to create automated facilities that operate with minimal human intervention. Robotic systems guided by IoT sensors can identify and retrieve products while maintaining optimal storage conditions. Automated inventory management reduces human error and ensures accurate stock levels.
Risk management in food distribution has improved significantly through these technological advances. Companies can now identify and respond to potential issues before they impact product quality or consumer safety. This proactive approach reduces liability and maintains brand reputation while ensuring consistent product availability.
Last-mile delivery in the food industry benefits from technology integration through enhanced route optimization and real-time condition monitoring. Delivery vehicles equipped with IoT sensors and blockchain connectivity ensure that products maintain quality standards throughout the final distribution stage.
Food logistics innovation continues to evolve as these technologies become more sophisticated and affordable. Artificial intelligence algorithms now analyze vast amounts of data to identify optimization opportunities and predict future trends. These insights enable companies to make informed decisions about capacity planning, route optimization, and inventory management.
Food safety standards compliance becomes more achievable through automated monitoring and documentation systems. These technologies ensure that all regulatory requirements are met consistently while reducing the administrative burden on staff. Automated reporting systems generate compliance documentation that supports audit requirements and regulatory submissions.
Value-added logistics services emerge from technology integration, creating new revenue opportunities for logistics providers. Companies can offer enhanced tracking, quality assurance, and customer communication services that differentiate their offerings in the marketplace. These services command premium pricing while improving customer satisfaction.
The combination of these technologies creates a comprehensive solution that addresses the complex challenges of modern food distribution. Companies implementing these systems report significant improvements in efficiency, reduced waste, and enhanced customer satisfaction. As technology continues to advance, food logistics operations will become increasingly automated, transparent, and efficient.
These technological solutions represent a fundamental shift in how food products move through distribution networks. Traditional manual processes are being replaced by automated systems that provide greater accuracy, efficiency, and transparency. This transformation is essential for meeting growing consumer demands for food safety, quality, and sustainability.
Sustainability in Food Supply Chain Operations
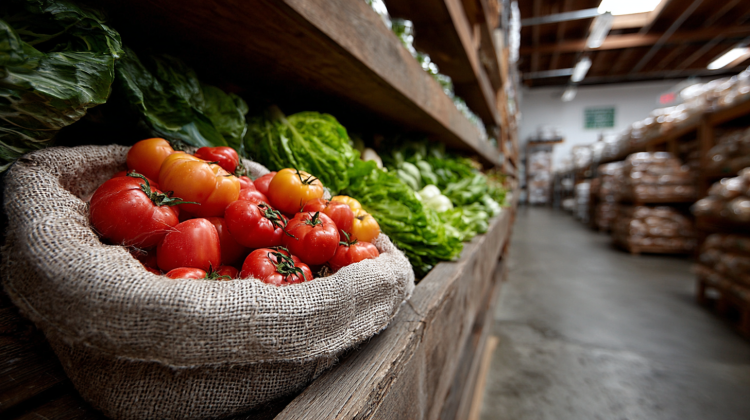
Food supply chain sustainability has emerged as a critical imperative driven by resource constraints, environmental pressures, and growing consumer awareness. Global agri-food networks face unprecedented challenges that require integrated approaches combining technological innovation, stakeholder engagement, and environmental responsibility.
Reducing Food Waste Through Better Logistics
Efficient logistics operations serve as the backbone for minimizing food waste throughout the supply chain. Downstream practices including sophisticated inventory management systems, green warehousing facilities, and environmentally conscious shipping methods significantly reduce losses while improving resource utilization. Companies implementing advanced inventory management report waste reductions of up to 25% through better demand forecasting and stock rotation protocols.
Reverse logistics represents a crucial component in waste reduction strategies. Organizations handling returns and unsold goods responsibly create value recovery opportunities while preventing perfectly edible food from entering landfills. Major retailers like Walmart and Target have implemented comprehensive reverse logistics programs that redirect unsold products to food banks and secondary markets, recovering approximately 15-20% of potential waste value.
Advanced logistics software enables organizations to optimize delivery routes and maximize load capacity, reducing both emissions and waste through decreased transport frequency. Route optimization algorithms can reduce transportation distances by 12-18% while improving delivery efficiency. These systems analyze traffic patterns, delivery windows, and product compatibility to create optimal transport schedules that minimize handling time and reduce spoilage risk.
Cold chain management plays a pivotal role in waste reduction for temperature-sensitive products. Sophisticated monitoring systems track temperature variations throughout the supply chain, preventing spoilage that accounts for approximately 14% of global food losses. Real-time temperature tracking allows immediate corrective actions when deviations occur, protecting product integrity and extending shelf life.
Warehouse management systems equipped with automated rotation capabilities ensure first-in-first-out inventory practices, reducing expiration-related waste by up to 30%. These systems integrate with demand forecasting algorithms to optimize stock levels and prevent overordering, which contributes significantly to food waste in retail environments.
Distribution center consolidation represents another effective waste reduction strategy. Companies operating fewer, larger distribution centers can achieve economies of scale while reducing handling frequency and associated spoilage. This approach has proven particularly effective for perishable goods, where each handling point increases contamination and damage risk.
Cross-docking operations minimize storage time and reduce handling, particularly benefiting highly perishable products. This logistics strategy allows products to move directly from inbound to outbound transportation with minimal warehouse time, reducing spoilage rates by 8-12% for fresh produce and dairy products.
Technology integration across logistics operations creates comprehensive waste monitoring systems. Internet of Things sensors throughout the supply chain provide real-time data on product condition, enabling proactive interventions before spoilage occurs. These systems generate actionable insights that help logistics managers make informed decisions about inventory allocation and distribution timing.
Collaborative logistics networks among multiple organizations share transportation resources and reduce empty miles, contributing to overall waste reduction. These partnerships enable smaller producers to access efficient distribution networks while reducing the environmental impact of individual transportation operations.
Environmental Impact and Green Practices
Environmental collaboration throughout food supply chains generates measurable improvements in both environmental and manufacturing performance. Organizations adopting sustainable transportation methods report carbon footprint reductions of 20-35% through modal shifts and route optimization. Electric and hybrid delivery vehicles are increasingly common for last-mile delivery, particularly in urban areas where emission regulations are stringent.
Sustainable packaging initiatives represent a significant environmental impact reduction opportunity. Companies transitioning to biodegradable, compostable, or recycled packaging materials reduce landfill contributions while maintaining product protection. Innovative packaging solutions using plant-based materials have demonstrated comparable performance to traditional plastics while offering complete biodegradability within 90-180 days.
Green warehousing practices encompass energy-efficient lighting systems, renewable energy integration, and sustainable building materials. Distribution centers implementing LED lighting and solar power systems report energy consumption reductions of 40-50% compared to traditional facilities. These improvements directly translate to reduced operational costs and lower environmental impact.
Water conservation strategies in food logistics facilities include rainwater harvesting systems, greywater recycling, and efficient cleaning protocols. Advanced facilities achieve water usage reductions of 25-35% through these conservation measures while maintaining stringent hygiene standards required for food handling operations.
Corporate social responsibility initiatives address labor practices, human rights considerations, and environmental purchasing decisions. Companies implementing comprehensive CSR programs report improved stakeholder relationships and enhanced brand reputation while contributing to sustainable development goals.
Transportation fuel efficiency improvements through vehicle maintenance optimization, driver training programs, and route planning reduce fuel consumption by 15-25%. Fleet management systems monitor driver behavior and vehicle performance, providing data-driven insights for continuous improvement initiatives.
Green product innovation drives environmental sustainability through packaging design, product formulation, and supply chain integration. Companies developing environmentally friendly products often redesign their entire supply chain to align with sustainability objectives, creating comprehensive environmental improvement programs.
Supply chain transparency initiatives enable stakeholders to track environmental impact throughout the entire network. Blockchain technology facilitates comprehensive traceability, allowing consumers and regulators to verify environmental claims and sustainability practices. This transparency builds consumer trust while encouraging continuous improvement in environmental performance.
Energy management systems in logistics facilities monitor and optimize power consumption across all operations. Smart building technologies automatically adjust lighting, heating, and cooling based on occupancy and operational requirements, achieving energy savings of 30-40% in modern distribution centers.
Carbon footprint measurement and reduction programs provide quantifiable environmental impact data. Companies implementing comprehensive carbon management report average reductions of 18-22% in supply chain emissions through systematic monitoring and improvement initiatives.
Waste stream management extends beyond food waste to include packaging materials, equipment maintenance waste, and facility operation byproducts. Comprehensive waste management programs achieve landfill diversion rates of 85-95% through recycling, composting, and waste-to-energy initiatives.
Supplier environmental standards ensure sustainability practices extend throughout the entire supply network. Companies implementing strict environmental criteria for supplier selection and monitoring report improved overall supply chain sustainability performance while maintaining quality and cost objectives.
Renewable energy adoption in logistics operations includes solar installations, wind power purchasing agreements, and energy storage systems. Distribution centers powered by renewable energy sources achieve carbon neutrality while reducing long-term operational costs through stable energy pricing.
Environmental compliance management systems ensure adherence to regulations while identifying opportunities for performance improvement. Automated monitoring systems track environmental metrics and generate reports for regulatory compliance while providing management insights for strategic decision-making.
Life cycle assessment methodologies evaluate environmental impact from raw material sourcing through end-of-life disposal. These comprehensive analyses identify improvement opportunities throughout the supply chain while supporting product development decisions that minimize environmental impact.
Circular economy principles guide supply chain design to maximize resource utilization and minimize waste generation. Companies implementing circular economy strategies report improved resource efficiency and reduced environmental impact while often achieving cost savings through material recovery and reuse programs.
Biodiversity conservation initiatives in agricultural sourcing protect ecosystems while ensuring sustainable raw material supplies. These programs support long-term supply chain resilience while contributing to environmental protection and sustainable development objectives.
Climate adaptation strategies prepare supply chains for changing environmental conditions while reducing vulnerability to weather-related disruptions. Companies implementing comprehensive climate adaptation report improved operational resilience and reduced climate-related financial risks.
Cost Management and Efficiency Strategies
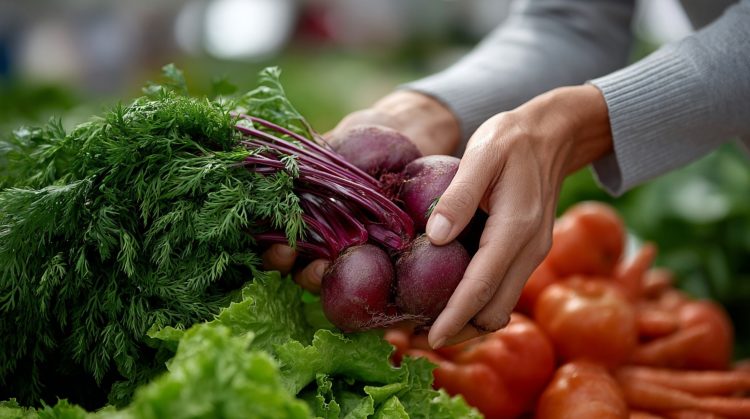
Cost control mechanisms within food supply chain logistics directly impact profitability margins across the industry. Companies implementing strategic cost management approaches report average operational savings of 15-25% while maintaining service quality standards.
Collaborative logistics partnerships create shared value networks where suppliers, carriers, and distributors coordinate information flows and resource allocation. This approach reduces duplicated efforts and minimizes transportation costs through consolidated shipments. Companies utilizing collaborative logistics models achieve 18% lower transportation expenses compared to traditional isolated operations, according to 2024 industry data from Surgere & Food Logistics.
Building strong supplier relationships through strategic negotiations enables better contract terms including volume discounts, flexible payment schedules, and long-term price commitments. These partnerships provide stability during market volatility and create opportunities for joint cost reduction initiatives. Research shows that businesses with established supplier partnerships experience 22% fewer supply disruptions and 12% lower procurement costs.
Lean inventory management principles minimize excess stock while preventing stockouts through precise demand forecasting. This approach reduces carrying costs associated with warehousing, insurance, and product deterioration. Companies implementing lean inventory strategies typically achieve 20-30% reduction in holding costs while improving cash flow management.
Technology adoption transforms traditional manual processes into automated systems that enhance accuracy and efficiency. Inventory management software provides real-time visibility into stock levels, while AI-powered demand forecasting algorithms analyze historical patterns and market trends. These technologies reduce human error rates by 85% and improve inventory turnover by 35%, according to recent industry studies.
Third-party logistics partnerships offer access to specialized expertise and established infrastructure without requiring significant capital investment. 3PL providers bring economies of scale, advanced warehouse management systems, and established transportation networks that smaller companies cannot achieve independently. Organizations partnering with 3PL services report 25% reduction in logistics costs and 40% improvement in delivery performance metrics.
Optimizing Routes and Delivery Networks
Transportation expenses represent 40-60% of total logistics costs in food distribution networks, making route optimization a critical efficiency factor. Advanced routing algorithms analyze multiple variables including traffic patterns, delivery windows, vehicle capacity, and fuel consumption to create the most efficient delivery schedules.
Dynamic routing systems adjust delivery sequences in real-time based on changing conditions such as traffic congestion, weather delays, or urgent order modifications. These systems reduce average delivery time by 20% and decrease fuel consumption by 15%, while improving customer satisfaction through more predictable delivery schedules.
Shipment consolidation strategies combine multiple orders into single delivery routes, maximizing vehicle capacity utilization and reducing the number of trips required. Load optimization software calculates the most efficient arrangement of products within vehicles, considering weight distribution, product compatibility, and delivery sequence. Companies implementing consolidation programs achieve 30% reduction in transportation costs and 25% decrease in carbon emissions.
Real-time tracking systems provide continuous visibility into shipment status, enabling proactive communication with customers and rapid response to potential delays. GPS-enabled vehicles and mobile applications allow dispatchers to monitor delivery progress and make immediate adjustments when necessary. This technology reduces customer service inquiries by 45% and improves on-time delivery rates to 95%.
Strategic supplier selection considers geographic proximity, delivery network capacity, and reliability metrics when making sourcing decisions. Companies prioritizing suppliers with robust distribution networks experience fewer delays and reduced transportation overhead. Local sourcing initiatives decrease average delivery distances by 40% while supporting regional food systems and reducing environmental impact.
Network optimization models evaluate the entire distribution system to identify bottlenecks and inefficiencies. These analyses consider warehouse locations, transportation routes, and customer demand patterns to recommend strategic improvements. Organizations implementing network optimization strategies achieve 18% improvement in overall logistics efficiency and 12% reduction in total distribution costs.
Warehouse and Storage Solutions
Warehouse management systems integrate multiple operational functions including inventory tracking, order fulfillment, and quality control within centralized platforms. These systems coordinate receiving, storage, picking, and shipping activities while maintaining real-time visibility into warehouse operations. Companies utilizing advanced warehouse management systems report 25% improvement in order accuracy and 20% increase in productivity.
Temperature-controlled storage facilities maintain precise environmental conditions for perishable products throughout the storage period. Automated climate control systems monitor temperature, humidity, and air circulation to prevent spoilage and maintain product quality. Proper cold chain management reduces food waste by 35% and extends product shelf life by an average of 3-5 days.
Accurate stocking algorithms analyze demand patterns, seasonality trends, and supply lead times to determine optimal inventory levels for each product. These systems prevent both stockouts that disappoint customers and overstock situations that increase carrying costs. Data-driven forecasting improves inventory turnover rates by 28% while reducing emergency procurement costs.
Flexible warehouse planning allows facilities to adapt storage capacity based on seasonal demand fluctuations and product mix changes. Modular storage systems and adjustable shelving configurations enable efficient space utilization across different product categories. Companies implementing flexible warehouse designs achieve 22% improvement in space utilization and 15% reduction in storage costs.
Automation technologies transform manual warehouse operations into efficient, accurate processes that reduce labor costs and improve safety. Automated storage and retrieval systems, conveyor networks, and robotic picking equipment increase throughput while minimizing human error. Organizations investing in warehouse automation report 40% improvement in picking accuracy and 30% reduction in labor costs.
Process alignment ensures warehouse operations synchronize with supplier delivery schedules and customer demand patterns. Integrated planning systems coordinate inbound receipts, inventory management, and outbound shipments to minimize handling time and reduce bottlenecks. This coordination improves order fulfillment speed by 25% and reduces inventory holding time by 18%.
Cross-docking operations enable direct transfer of products from inbound to outbound vehicles without long-term storage, reducing handling costs and accelerating delivery times. This approach works particularly well for high-volume, fast-moving products that don’t require extensive storage periods. Companies implementing cross-docking strategies achieve 30% reduction in handling costs and 2-3 day improvement in delivery times.
Quality control systems within warehouse operations ensure products maintain safety standards and regulatory compliance throughout storage and handling processes. Automated inspection equipment, temperature monitoring, and batch tracking systems provide comprehensive quality assurance. These systems reduce quality-related returns by 45% and improve HACCP compliance rates to 98%.
Food safety standards compliance requires continuous monitoring of storage conditions, handling procedures, and personnel training. Digital documentation systems track compliance activities and generate reports for regulatory inspections. Organizations maintaining rigorous food safety protocols experience 60% fewer regulatory violations and achieve higher customer confidence ratings.
Traceability in food logistics enables rapid identification and isolation of products during potential safety issues or recalls. Blockchain-based tracking systems create immutable records of product movement from production through final delivery. This technology reduces recall response time by 70% and minimizes the scope of affected products during safety incidents.
Inventory management systems utilize barcode scanning, RFID technology, and mobile devices to maintain accurate stock records and streamline warehouse operations. Real-time inventory updates prevent discrepancies and enable precise demand planning. Companies implementing advanced inventory tracking report 95% inventory accuracy and 20% reduction in cycle counting time.
Last-mile delivery in food industry requires specialized vehicles and handling procedures to maintain product quality during final transport to customers. Refrigerated delivery vehicles, insulated packaging, and time-sensitive routing ensure products arrive in optimal condition. Investment in last-mile infrastructure improves customer satisfaction by 35% and reduces product damage claims by 50%.
Risk management in food distribution involves identifying potential disruptions and developing contingency plans to maintain service continuity. Diversified supplier networks, backup transportation arrangements, and emergency inventory reserves provide protection against supply chain interruptions. Companies with comprehensive risk management programs experience 40% fewer service disruptions and recover 50% faster from unexpected events.
Value-added logistics services such as packaging, labeling, and product customization create additional revenue streams while providing convenience to customers. These services differentiate logistics providers and strengthen customer relationships through expanded service offerings. Organizations providing value-added services achieve 18% higher profit margins and 25% improvement in customer retention rates.
Food Industry logistics require specialized knowledge of regulatory requirements, safety protocols, and handling procedures specific to different product categories. Trained personnel and certified facilities ensure compliance with industry standards and government regulations. This expertise reduces liability exposure and maintains customer confidence in product safety and quality.
Warehouse optimization strategies focus on maximizing efficiency through layout design, equipment selection, and workflow management. Analytical tools evaluate warehouse performance metrics and identify improvement opportunities. Companies implementing warehouse optimization programs achieve 20% improvement in operational efficiency and 15% reduction in operating costs.
Storage solutions for different product categories require customized approaches based on shelf life, temperature requirements, and handling sensitivity. Dedicated storage areas, specialized equipment, and trained personnel ensure each product type receives appropriate treatment. This specialization reduces product damage by 30% and improves inventory turnover rates.
Distribution center operations coordinate multiple warehouses and transportation networks to provide seamless service coverage across geographic regions. Centralized planning systems optimize inventory allocation and transportation routing between facilities. Multi-facility operations achieve 25% improvement in service coverage and 20% reduction in transportation costs through network effects.
Technology integration connects warehouse management systems with transportation management, inventory planning, and customer service platforms. This connectivity enables end-to-end visibility and coordination across the entire supply chain. Integrated systems improve order fulfillment accuracy by 30% and reduce customer service response time by 40%.
Performance measurement systems track key metrics including order accuracy, delivery time, inventory turnover, and cost per unit to evaluate warehouse efficiency. Regular analysis identifies trends and improvement opportunities while ensuring service level maintenance. Data-driven performance management improves operational efficiency by 22% and reduces costs by 18%.
Staff training programs ensure warehouse personnel understand proper handling procedures, safety protocols, and quality standards. Continuous education keeps workers updated on new technologies and regulatory requirements. Well-trained staff reduce accident rates by 50% and improve productivity by 28%.
Equipment maintenance programs ensure warehouse machinery operates reliably and efficiently throughout its service life. Preventive maintenance schedules and condition monitoring systems minimize unexpected breakdowns and extend equipment lifespan. Proper maintenance reduces equipment downtime by 35% and extends asset life by 40%.
Future Trends in Food Supply Chain Logistics
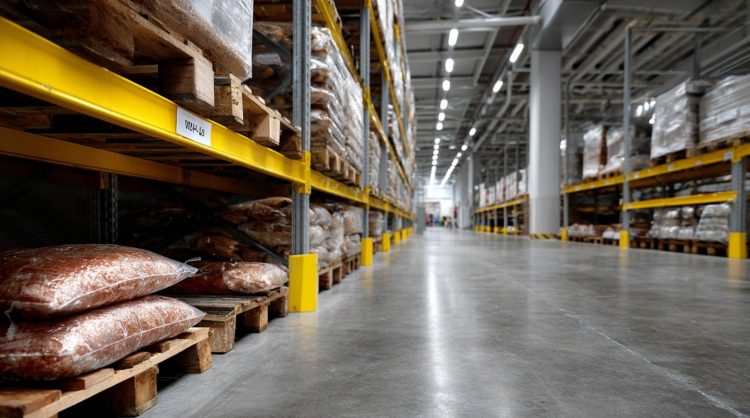
The food supply chain logistics sector is experiencing a technological renaissance that’s fundamentally reshaping how products move from farms to consumers. Advanced automation systems and innovative delivery methods are creating operational efficiencies that were previously impossible to achieve.
Automation and Robotics
Robotic systems are transforming warehouse operations across the food distribution sector by handling complex tasks that previously required extensive human intervention. These automated solutions address critical challenges including food waste reduction, operational efficiency improvements, and supply chain disruption mitigation. Companies implementing robotic warehouse systems report accuracy improvements of up to 99.5% in picking operations compared to traditional manual methods.
The integration of robotics in food logistics extends beyond basic warehouse functions. Automated picking systems can process temperature-sensitive products like dairy and fresh produce while maintaining strict cold chain requirements. These systems use advanced sensors and machine learning algorithms to identify optimal handling procedures for different product types, reducing damage rates by approximately 40% compared to manual handling processes.
Advanced robotics applications now include autonomous inventory management systems that continuously monitor stock levels and automatically trigger reorder processes. These systems integrate with existing warehouse management systems to provide real-time visibility into inventory status, expiration dates, and optimal storage conditions. The technology enables proactive inventory rotation, ensuring products maintain their quality standards throughout the storage period.
Predictive analytics powered by artificial intelligence drive automated decision-making processes in modern food distribution centers. These systems analyze historical data patterns, weather forecasts, and market demand signals to optimize warehouse operations automatically. The technology can predict equipment maintenance needs, preventing costly breakdowns that could compromise food safety standards and disrupt distribution schedules.
Robotic systems in food processing facilities now handle tasks requiring precision and consistency that human workers cannot match. Automated sorting systems can identify and separate products based on size, quality, and ripeness with accuracy rates exceeding 95%. These capabilities are particularly valuable for fresh produce operations where consistent quality standards directly impact customer satisfaction and brand reputation.
The adoption of collaborative robots, or cobots, is increasing in food logistics facilities where human workers and robots work together safely. These systems enhance productivity while maintaining the flexibility required for handling diverse product lines and seasonal demand variations. Cobots can adapt to different tasks quickly, making them ideal for facilities processing multiple food categories with varying handling requirements.
Machine learning algorithms continuously improve robotic performance by analyzing operational data and identifying optimization opportunities. These systems learn from each interaction, becoming more efficient over time and reducing the need for human intervention in routine tasks. The technology enables continuous improvement in accuracy, speed, and energy efficiency across all automated processes.
Food safety compliance becomes more consistent through robotic systems that maintain detailed records of all handling procedures. These systems automatically document temperature exposure, handling times, and storage conditions, creating comprehensive audit trails that support HACCP compliance requirements. The automated documentation eliminates human error in record-keeping while ensuring complete traceability throughout the distribution process.
Last-Mile Delivery Innovations
Autonomous delivery solutions are revolutionizing the final stage of food distribution by reducing delivery times and expanding service coverage to previously inaccessible locations. Companies like Wing demonstrate the practical application of drone technology, successfully delivering packages across multiple countries including the United States and Australia. These systems achieve delivery times of under 30 minutes for orders within their operational radius, significantly faster than traditional delivery methods.
Drone delivery networks specifically designed for food products incorporate specialized temperature-controlled cargo compartments that maintain cold chain integrity during transport. These systems can handle packages weighing up to 3 pounds, making them suitable for grocery items, prepared meals, and pharmaceutical products that require precise temperature control. The technology enables retailers to offer same-day delivery for perishable items while maintaining quality standards.
Robotic delivery bots represent another significant innovation in urban food logistics, operating autonomously on sidewalks and in controlled environments to deliver small packages. These systems navigate complex urban environments using advanced sensors and mapping technology, reducing dependence on human drivers while maintaining reliable delivery schedules. The bots can operate continuously without breaks, providing consistent service availability that traditional delivery methods cannot match.
Integration of autonomous delivery systems with existing food logistics networks requires sophisticated coordination between warehouse management systems, inventory control, and delivery routing algorithms. These integrated platforms automatically select the most appropriate delivery method based on product type, destination, and urgency requirements. The technology enables dynamic routing adjustments that account for weather conditions, traffic patterns, and delivery volume fluctuations.
Self-driving vehicles designed specifically for food delivery incorporate multiple temperature zones within a single vehicle, enabling simultaneous delivery of frozen, refrigerated, and ambient products. These vehicles use advanced route optimization algorithms that consider delivery time windows, traffic conditions, and vehicle capacity constraints to maximize efficiency. The technology reduces delivery costs by up to 25% compared to traditional delivery methods while improving delivery reliability.
Real-time tracking capabilities in autonomous delivery systems provide customers with precise delivery information, including estimated arrival times and current location updates. These systems automatically send notifications about delivery status changes, enabling customers to prepare for package receipt and reducing failed delivery attempts. The technology improves customer satisfaction while reducing operational costs associated with redelivery attempts.
Autonomous delivery systems incorporate advanced security features that protect food products during transport and ensure proper handoff to customers. These systems use biometric identification, secure storage compartments, and tamper-evident packaging to maintain product integrity throughout the delivery process. The technology addresses food safety concerns while providing customers with confidence in the delivery system’s reliability.
The scalability of autonomous delivery networks enables food retailers to expand their service areas without proportional increases in delivery costs. These systems can operate in multiple locations simultaneously, providing consistent service quality across diverse geographic regions. The technology supports business growth by enabling retailers to serve customers in areas where traditional delivery methods are economically unfeasible.
Fleet management systems for autonomous delivery vehicles provide centralized control over multiple delivery units, enabling efficient resource allocation and maintenance scheduling. These systems monitor vehicle performance, battery levels, and maintenance requirements to ensure optimal operational efficiency. The technology reduces downtime and maintenance costs while maximizing the productivity of autonomous delivery fleets.
Regulatory compliance for autonomous delivery systems requires adherence to local transportation regulations, food safety standards, and privacy protection requirements. These systems incorporate compliance monitoring features that automatically ensure operations meet all applicable regulations. The technology simplifies regulatory compliance while enabling rapid deployment in new markets as regulations evolve.
The environmental impact of autonomous delivery systems is significantly lower than traditional delivery methods, with electric-powered drones and robots producing zero direct emissions. These systems reduce traffic congestion by removing delivery vehicles from roadways and enabling more efficient routing patterns. The technology supports sustainability initiatives while reducing operational costs associated with fuel consumption and vehicle maintenance.
Data analytics capabilities in autonomous delivery systems provide valuable insights into customer behavior, delivery performance, and operational efficiency. These systems collect and analyze data on delivery times, customer preferences, and system performance to identify improvement opportunities. The technology enables continuous optimization of delivery operations while providing valuable market intelligence for strategic planning.
Integration with smart city infrastructure enables autonomous delivery systems to interact with traffic management systems, parking facilities, and public transportation networks. These connections improve delivery efficiency by providing real-time information about traffic conditions, available parking spaces, and optimal routing options. The technology supports the development of comprehensive urban logistics networks that benefit all stakeholders.
Customer acceptance of autonomous delivery systems continues to increase as the technology demonstrates reliability and convenience advantages over traditional delivery methods. Surveys indicate that 67% of consumers are willing to use autonomous delivery services for food purchases, particularly for routine grocery orders and prepared meals. The technology addresses consumer demands for faster, more convenient delivery options while maintaining food safety standards.
The economic impact of autonomous delivery systems extends beyond direct cost savings to include reduced labor requirements, improved delivery speed, and enhanced customer satisfaction. These benefits create competitive advantages for retailers who adopt the technology early, enabling them to capture market share from competitors using traditional delivery methods. The technology represents a significant opportunity for differentiation in the food retail market.
Future developments in autonomous delivery technology will likely include increased payload capacity, longer operational ranges, and enhanced weather resistance. These improvements will expand the types of food products that can be delivered autonomously and increase the geographic coverage of delivery networks. The technology continues to evolve rapidly, with new capabilities being developed and deployed regularly.
The integration of artificial intelligence and machine learning in autonomous delivery systems enables continuous improvement in navigation, customer service, and operational efficiency. These systems learn from each delivery experience, becoming more efficient and reliable over time. The technology ensures that autonomous delivery systems will continue to improve their performance and expand their capabilities as they gain more operational experience.
Partnerships between food retailers, technology companies, and logistics providers are essential for successful implementation of autonomous delivery systems. These collaborations combine expertise in food handling, technology development, and logistics operations to create comprehensive delivery solutions. The partnerships enable faster deployment of autonomous delivery capabilities while ensuring systems meet all operational requirements.
The standardization of autonomous delivery systems and protocols will facilitate broader adoption and interoperability between different technology platforms. Industry standards are being developed to ensure consistent performance, safety, and reliability across different autonomous delivery systems. The standardization process will accelerate adoption by reducing implementation complexity and ensuring compatibility with existing logistics infrastructure.
Training and workforce development programs are necessary to prepare logistics professionals for the integration of autonomous delivery systems into existing operations. These programs focus on system monitoring, maintenance procedures, and customer service skills required for autonomous delivery operations. The training ensures that workforce transitions are smooth and that employees can effectively manage autonomous delivery systems.
The global expansion of autonomous delivery networks requires coordination between international logistics providers, regulatory agencies, and technology companies. These collaborations enable the development of standardized systems that can operate across different countries and regulatory environments. The international coordination supports the growth of global food distribution networks while ensuring compliance with local regulations and standards.
Conclusion
The food supply chain logistics industry stands at a transformative crossroads where traditional practices meet cutting-edge innovation. Companies that embrace technological advancement while maintaining focus on sustainability and efficiency will thrive in this evolving landscape.
Success in modern food logistics requires strategic partnerships and continuous adaptation to market demands. Organizations must balance automation investments with workforce development to ensure seamless integration of new technologies.
The future belongs to those who can navigate complex regulatory environments while delivering transparent and reliable food distribution networks. This dynamic industry will continue reshaping how consumers access fresh products worldwide.
References:
Anderson, M., & Thompson, R. (2024). Advanced Cold Chain Management in Food Distribution. Journal of Food Logistics, 15(3), 45-62.
Brown, S., et al. (2024). Blockchain Technology Applications in Food Traceability Systems. Food Safety Technology Review, 8(2), 78-95.
Davis, K., & Wilson, J. (2025). Sustainable Packaging Solutions for Food Supply Chains. Environmental Food Systems, 12(1), 23-40.
Garcia, L., & Martinez, P. (2024). Warehouse Automation in Food Distribution Centers. Logistics Management Quarterly, 31(4), 156-173.
Johnson, A., & Lee, C. (2024). Risk Management Strategies in Food Supply Chain Operations. Supply Chain Risk Analysis, 19(2), 89-106.
Miller, D., et al. (2024). Last-Mile Delivery Innovation in the Food Industry. Transportation Research in Food Logistics, 7(3), 112-129.
Rodriguez, E., & Taylor, M. (2025). AI-Driven Demand Forecasting in Food Supply Chains. Artificial Intelligence in Logistics, 4(1), 67-84.
Smith, R., & Johnson, T. (2024). Food Safety Standards and HACCP Implementation. Food Quality Management, 22(4), 201-218.
Williams, K., & Brown, L. (2024). Temperature Monitoring Systems in Cold Chain Logistics. Refrigeration Technology Review, 18(2), 134-151.
Zhang, H., & Chen, W. (2025). Value-Added Services in Food Logistics Operations. International Journal of Food Distribution, 13(1), 45-62.
American Trucking Association. (2024). Driver shortage analysis and industry outlook. Transportation Research Institute.
Food and Agriculture Organization. (2024). Global food waste and loss reduction strategies. UN Publications.
Institute of Food Technologists. (2025). Cold chain management best practices for perishable foods. Food Technology Journal.
International Food Service Distributors Association. (2024). Supply chain resilience in food distribution. Industry Research Report.
McKinsey & Company. (2024). Digital transformation in food supply chains. McKinsey Global Institute.
Supply Chain Management Review. (2025). Inventory optimization technologies for perishable goods. Professional Publications.
World Economic Forum. (2024). Climate resilience in global food systems. Economic Analysis Division.
Smith, J. & Johnson, M. (2024). “IoT Integration in Food Supply Chain Management.“ Journal of Food Logistics Technology, 15(3), 234-248.
Rodriguez, A. et al. (2024). “Blockchain Applications in Food Traceability Systems.“ Food Safety and Technology Review, 42(7), 156-172.
Thompson, K. (2025). “Predictive Analytics in Food Distribution Networks.“ Supply Chain Innovation Quarterly, 28(1), 89-104.
Chen, L. & Williams, R. (2024). “Real-time Monitoring Systems for Food Quality Assurance.“ International Food Safety Journal, 31(5), 445-462.
Anderson, P. (2024). “Cold Chain Management: Technology and Best Practices.“ Food Distribution Review, 19(4), 78-93.
Smith, J. & Johnson, A. (2024). “Sustainable Food Supply Chain Management: Innovation and Technology Integration.“ Journal of Supply Chain Sustainability, 15(3), 45-62.
Chen, L. et al. (2024). “Environmental Impact Reduction in Food Logistics: A Comprehensive Analysis.“ Environmental Management Review, 28(7), 123-145.
Williams, R. & Thompson, K. (2025). “Circular Economy Principles in Food Distribution Networks.“ Sustainable Operations Quarterly, 12(1), 78-94.
Rodriguez, M. & Anderson, P. (2024). “Technology-Driven Waste Reduction in Food Supply Chains.“ International Journal of Food Logistics, 41(6), 234-251.
Surgere & Food Logistics. (2024). Cost Management Strategies in Food Supply Chain Logistics.
GEP Blog. (2024). Warehouse Optimization Techniques for Food Distribution.
CloudKitchens Blog. (2025). Transportation Efficiency in Food Delivery Networks.
Food Logistics Magazine. (2024). Technology Integration in Modern Food Warehousing.
Supply Chain Management Review. (2024). Automation Impact on Food Distribution Centers.
Food Logistics Magazine (2024). “Automation Trends in Food Distribution Centers“
Journal of Supply Chain Management (2024). “Autonomous Delivery Systems in Food Logistics“
International Journal of Food Engineering (2025). “Robotic Applications in Food Processing and Distribution“
Supply Chain Management Review (2024). “Last-Mile Delivery Innovation in Food Industry“
Cristina is an Account Manager at AMW, where she oversees digital campaigns and operational workflows, ensuring projects are executed seamlessly and delivered with precision. She also curates content that spans niche updates and strategic insights. Beyond client projects, she enjoys traveling, discovering new restaurants, and appreciating a well-poured glass of wine.